Ever since the movie debuted, I've had the Starship Troopers Mobile Infantry costume on my cosplay bucket list. When the production-used props and costumes went up for auction I didn't get wind of it until well after all of the bidding was over and there was no way I could get any for myself.
Then, back in 2019, my Southern California based friend J.P. Pollio lent me his screen-used set of Starship Troopers armor so I could use it as a template to make replicas of my own. The plan was to build a whole squad of Mobile Infantry troopers in time for San Diego Comic Con that year.
Of course, we were also making our Sisters of Battle squad and that build ended up overtaking everything else in the world while I was screaming toward the deadline.
So the Starship Troopers gear stayed in the box and when I asked J.P. if he wanted it back when we were all in San Diego, even though I hadn't gotten around to making my copies. He said he wasn't worried about it. We'd just go ahead and do a squad cosplay next year.
Then, in the beginning of the next year, the world came to a sudden, screeching halt. With the COVID-19 pandemic in full swing, big, crowded events like San Diego Comic Con, already a notorious haven for the spread of viruses of all kinds, were cancelled or postponed in the interest of public health. It would be two years before the full-scale event would happen in person again. In that time, since nobody was going out in costume to any events, the box of screen-used armor sat on the shelf and was largely forgotten.
Then, in 2023, J.P. asked if I could hand it off to him when we met up at Wondercon in Anaheim. "No problem," says I, "I'll go load it into the car now." Then I loaded it into the car.
We caught up several times over the course of that event and each time I say him I said, "let's go grab your box," and he'd say something like, "we'll get to it."
Then we didn't get to it. I was halfway through the six-hour drive home when it occurred to me that his box was still in the car.
So this year, about a month before Wondercon, J.P. asks if I can bring it back again. This time, since I wasn't too too busy, I'd have time to make my own masters based on exacting measurements of the original parts and still be able to get him back his stuff.
I started by making a copy of the lower back plate out of 1/2" MDF with some 1/4" MDF details layered on top:
Fully assembled and glued together, the lower back looked like so:

To minimize the time spent sanding and filling the edges, the bevels were soaked with a tiny bit of thin CA glue in order to seal them up:

Here's a comparison shot showing my MDF master alongside the screen-used back plate:

Here I am being all smug and self-satisfied about it:

The edges were blended in a bit more using some glazing and spot putty:

After a couple of rounds of putty and sanding, I was pretty happy with it:

It would go on to receive two or three coats of grey primer:

At this point, I was thrilled with the progress. Geri the Husky* was not impressed:

The waist section was a tiny bit more complicated to make. I still started with the overall shape in 1/2" MDF, but then I also added a layer of 1/8" foamed PVC to get the recesses I needed before adding the raised details in 1/4" MDF:
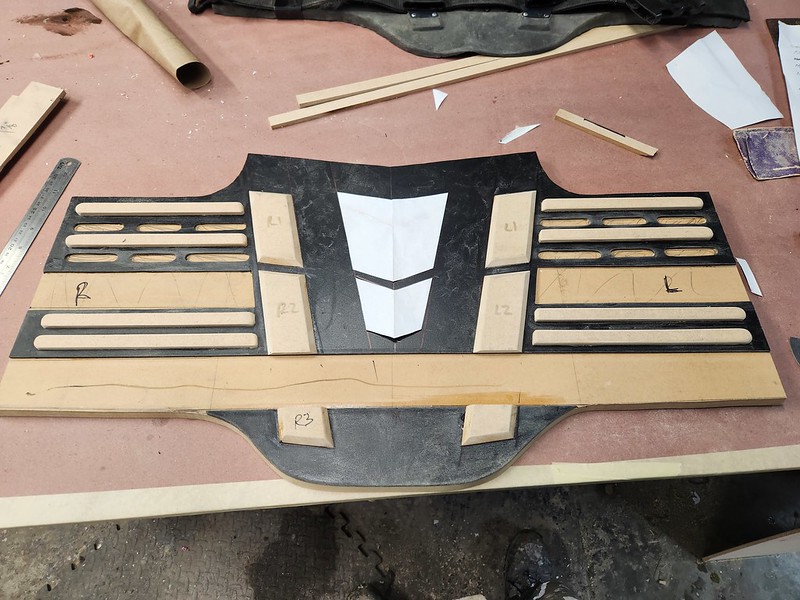
Here it is after the first coat of primer:

And alongside the screen-used pieces:

The collar, or shoulder piece was done in the same manner. It was made more difficult by the fact that I didn't want to undo the seam at the left shoulder, so I had to do a bit of creative stretching and bending it to determine the exact shape of the overall outline:

Here's Rachel doing the last round of filling and sanding to smooth out the fully-build shoulder/chest section:

With all three parts in primer, things were looking pretty good:

Then they'd get a couple of coats of shiny lightish read paint:

And there they were left to dry for a couple of days to ensure the paint wouldn't affect the mold rubber at all. Shiny:

Geri the Husky* was still unimpressed:

Since there was no way to make the MDF parts wearable, would have to make a mold and cast them in something else. The first step in moldmaking was to mount each piece onto a flat board and build a cardboard wall around the part, leaving about an inch of margin all the way around the edges:

All three pieces were set up this way:
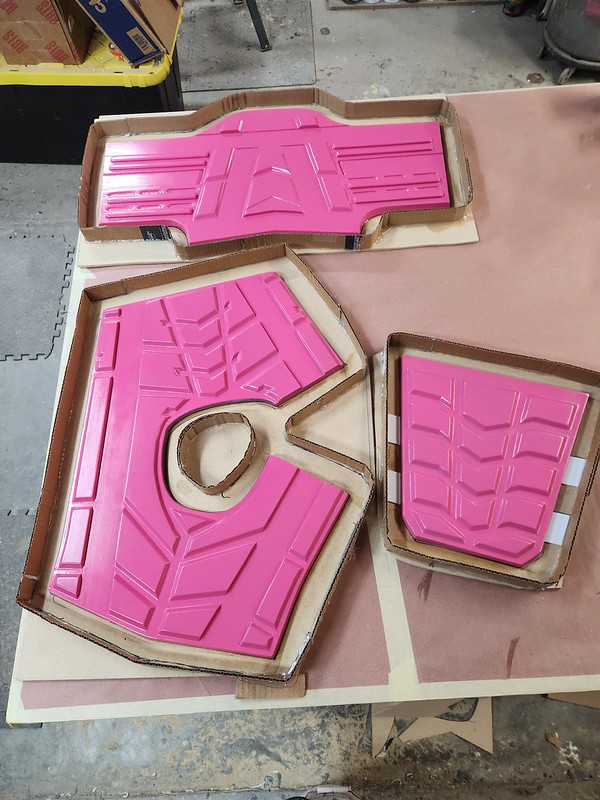
Then it was just a matter of mixing up a metric butt-ton of silicone rubber and pouring the molds:

The table was shimmed to make it all sit perfectly level while the rubber cured overnight:

The following morning, I removed the rubber molds from the parts:


To ensure adequate mixing and give it additional aeration to encourage expansion a bit, I mix the foam with a mechanical mixer for a solid 20 seconds making sure to scrape the sides of the container with the mixer to blend in any residue of part A or part B clinging to the sides:

Then it's on to pouring the foam into the mold:

In order to make sure there are no visible voids at the edges, I start by pouring along the edges first:

Then I finish by pouring whatever's left in the bucket over the open field in the middle of the mold:

As long as I've mixed the right amount of foam, it will expand to fill the whole mold, but if there's going to be any parts that are missing a bit of thickness, it'll be better to have them somewhere in the middle where nobody can see them.
As the foam begins to expand, I lay a piece of stretch knit fabric over the top:

This is basically T-shirt fabric that I'm using to reinforce the rubber:

This particular foam that I'm using is pretty durable stuff, but since the strap brackets will be riveted on later, I need to give the rivets and washers something a big more substantial to grab onto.
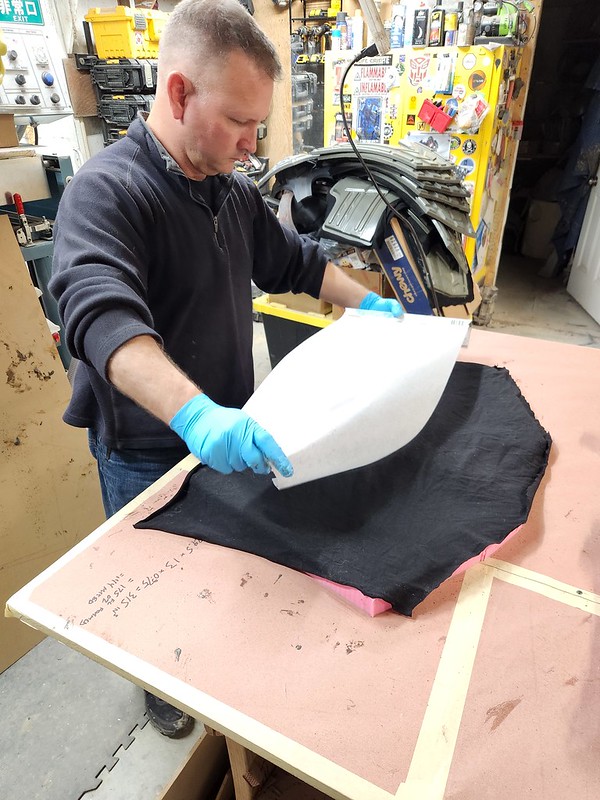
This is my last chance to make sure there are no wrinkles in the backing fabric:

The wax paper ensures that any foam that gets forced through the weave of the fabric as it's expanding won't glue itself to the board that I lay on top for back pressure:

To keep the foam from overflowing the edges of the mold as it expands and help it lock into the fibers of the fabric, I place sandbags on top of the board:
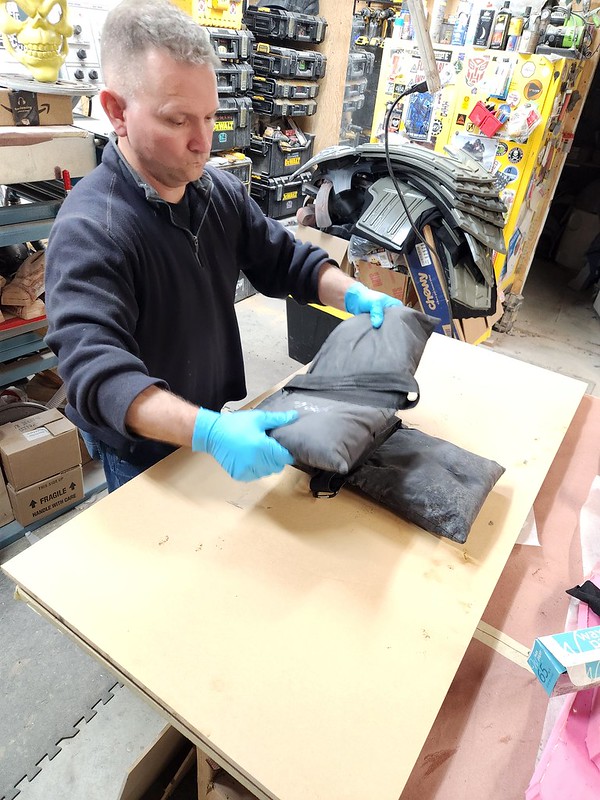
Lots of sandbags:

After about 90 minutes, the foam has cured and the part can be de-molded:
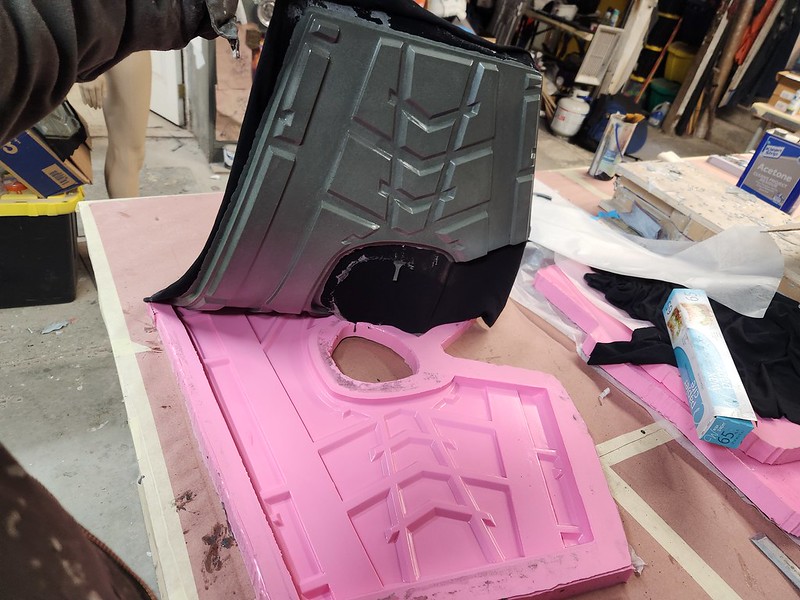
My coloration isn't a perfect match for the screen-used part, but I'm pretty happy with it:

Of course, when I throw it on the pile of castings, I can see how variable my coloration method is:

Besides, the parts will end up being painted anyway.

I definitely feel like I'm on the right track:

Geri the Husky* is still not impressed:

Stay tuned...
Looking forward to more in this series. I want to know more.
ReplyDelete