Since I'm determined to do a series of articles about my methods, this project will serve as a great example of how I use my Craftsman Carvewright CNC machine to build props. For those of you just tuning in, I bought this machine secondhand almost two years ago. It's temperamental and a bit frustrating sometimes, but when everything works it makes life a lot easier.
In this case, I used it to create the prototype for these:
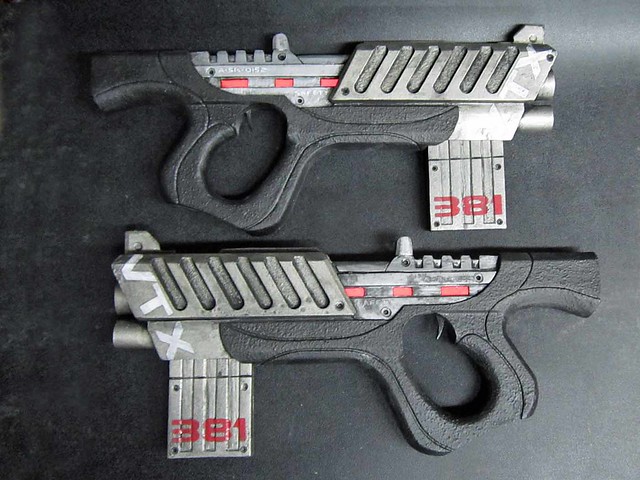
Read on for a step-by-step process of how they were turned from bits and bytes into practical prop weapons.
Here's what the original render looked like when the modeller sent it to me:
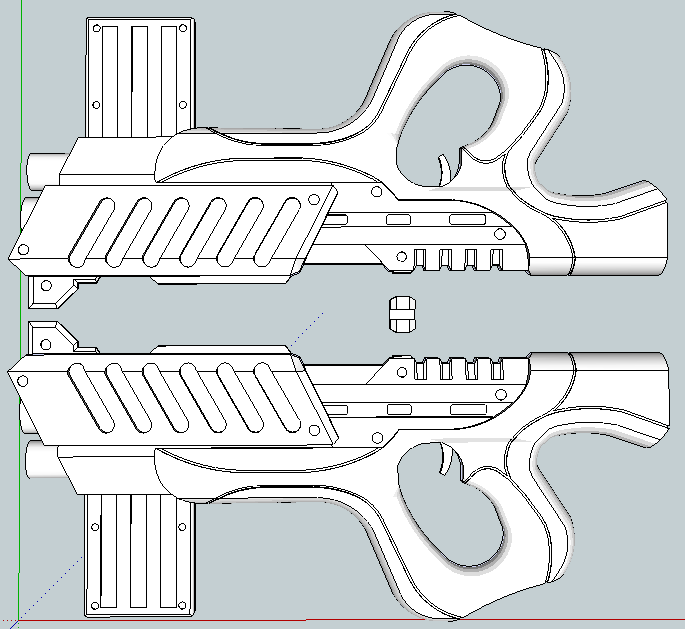
I was floored. The model was so well done and the level of detail was so complete, there was almost nothing for me to do but cut it up and feed it to Lopez the Robot Whittler. Lopez is the CNC machine, named after the robot character in the popular webseries Red vs. Blue.
Making this file into something that Lopez could cut out was a job for the .stl importer in the proprietary software that comes with the Carvewright:
Since Lopez is only a 3-axis CNC machine and can only make a 3/4-inch deep cut, I had to slice the model into 3/4" thick pieces. After deciding where best to slice the model, all that was left was to lay it out on a couple of virtual boards and upload the carving projects to the machine.
Here he is spitting out one of the first slices:
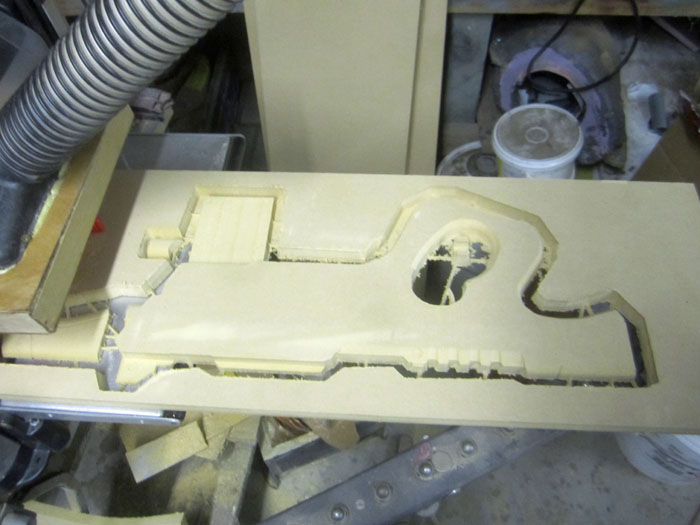
Here's the first half out of the machine:
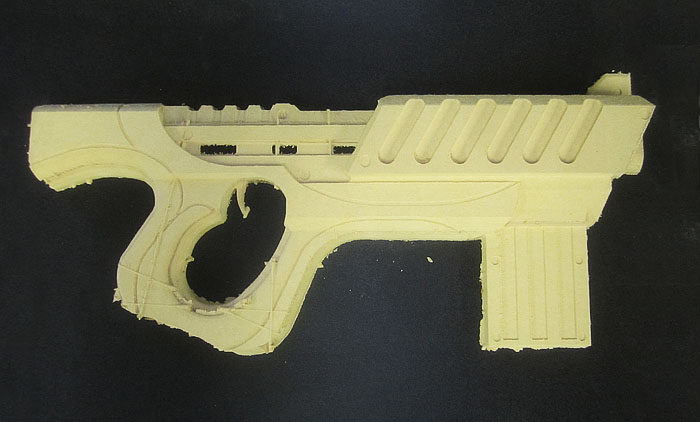
The first build ended up being way too big. Here it is made to look bigger in the hands my very small nephew:
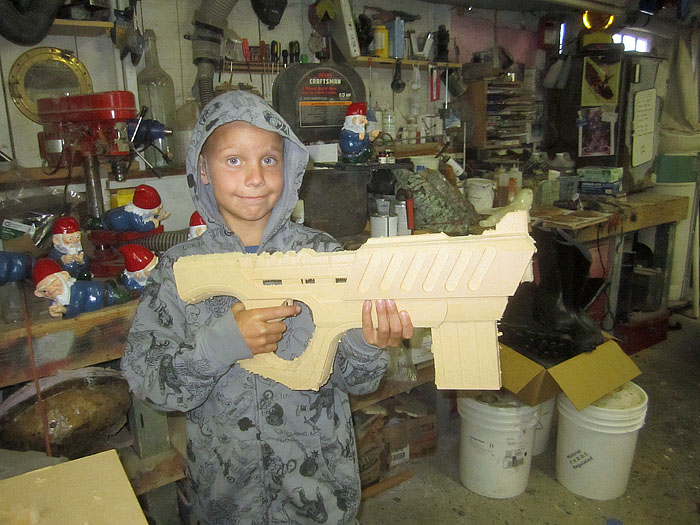
So threw out the first version* and asked the modeller to re-scale the whole thing and work it out so the magazine could be removable. Here's the second carve in my perfectly medium-sized hand for scale:
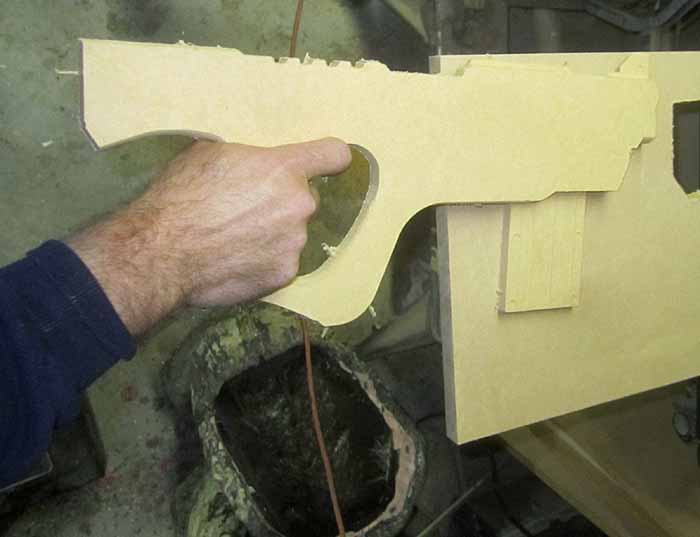
Much better:
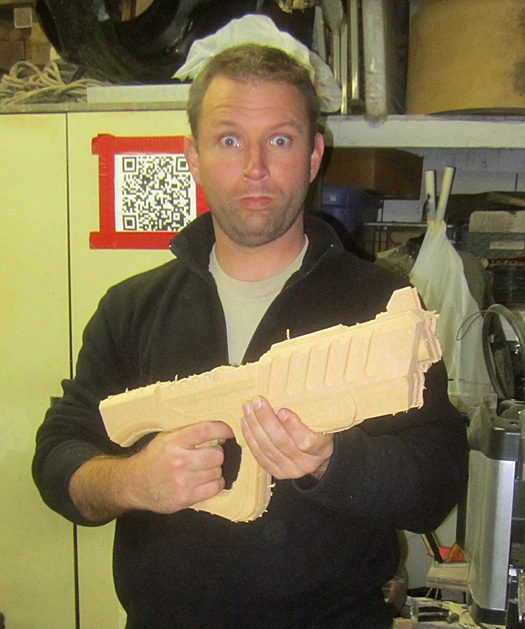
With all four slices of the main body cut out, Lopez' involvement in the project is finished. Now it was up to me to smooth everything out and add any details too small for Lopez to carve out with his 1/16" round-tipped carving bit.
I also had to decide how best to open it up so I could wire it up with lights and whatnot. After a lot of time spent staring at the parts, I decided on making the main body with two separate panels. One would be glued on during assembly after the lights were installed and the other would be held in place with magnets so it could be opened to access the batteries and such.
Here's a shot of the parts all glued up after I'd cut the side panels off of the left side:

Once the epoxy had set up, all that was left was to give it a few coats of primer to make the surface ready for finishing. Finishing the prototype amounted to sanding down the parts that needed to be smooth and priming it all:

Then I re-grooved the grooves in the grips with a loose jigsaw blade and added some textured paint to make it rough:
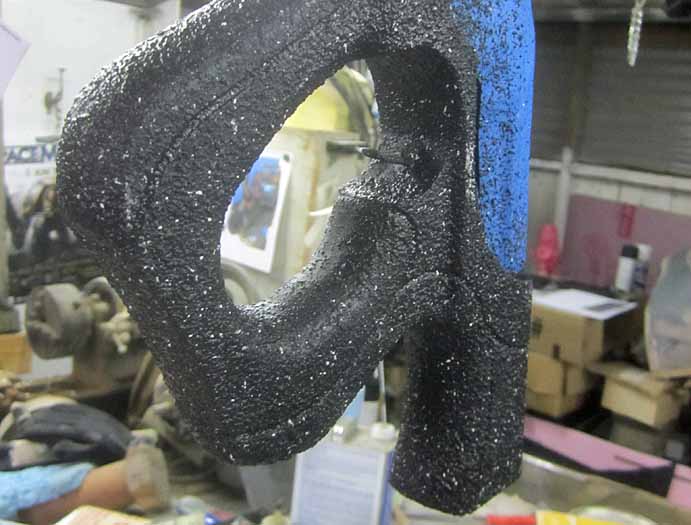
Here's the end result with some vinyl decals added on to raise the lettering on either side of the piece:
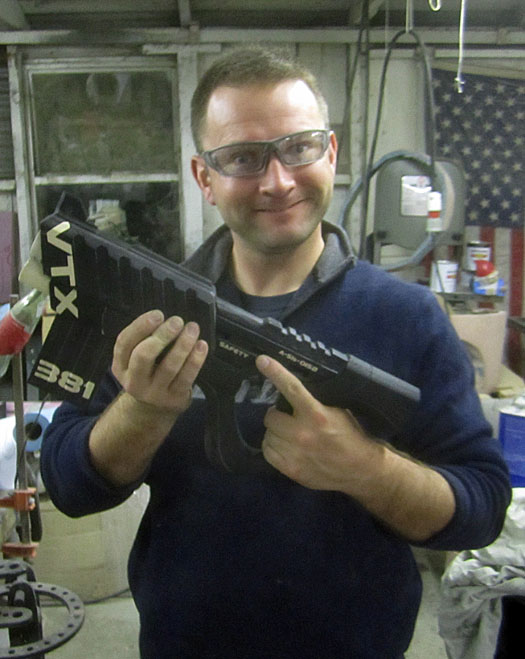
The last thing I had to do was to make up the double-barrel arrangement for the front end:
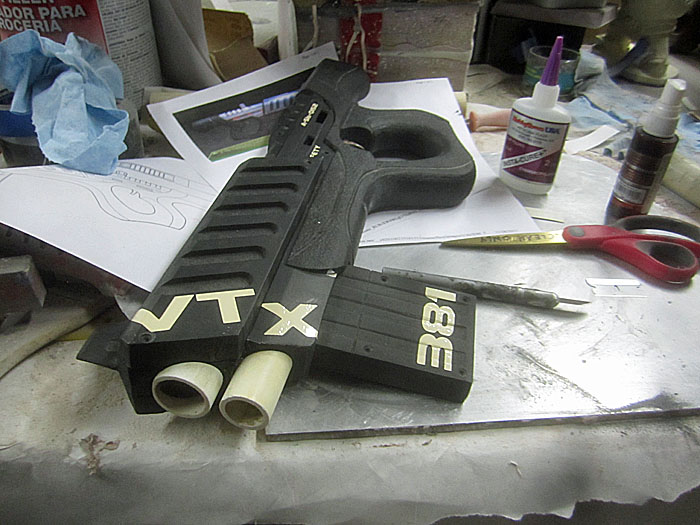
If I'd painted the piece in the correct colors, I could call it done at this stage. But, because I rarely make one of anything, I had to make a mold. This way I could send one to the modeller while still keeping one for myself.
Molding was done in much the same way as my Mass Effect M-3 Predator Pistol, but you could do it the same way I did my HALO 3 Assault Rifle too. Here's a shot of me pouring rubber for the first half of the mold:
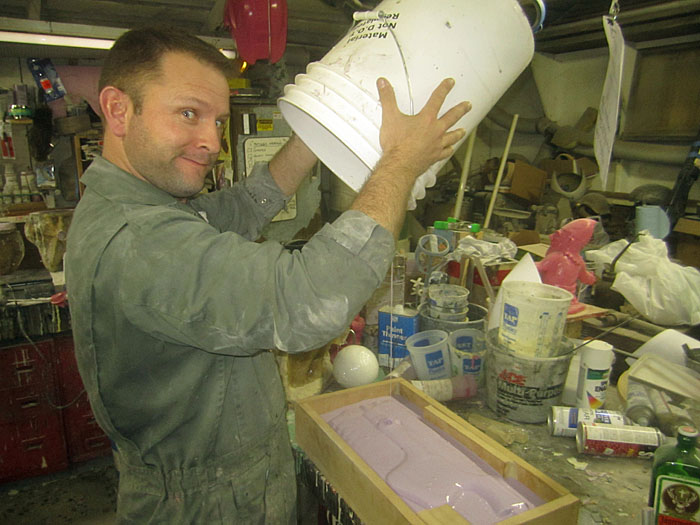
The first casting out of the mold was perfect:
As were the next few:
After I picked one to mail to the modeller I picked the best two to finish. Here they are all painted up:
For the lighting I used electroluminescent tape (also called EL tape). It made sense in this case because I wanted an even glow across all three of the lights on either side above the grip. The only problem is that when I buy EL tape (from www.glowhut.com) it's typically sold in 3-foot lengths with electrical leads attached on one end and an inverter to power it. Since this project called for a pair of four-inch lengths, I would have to make some modifications.
EL tape is not very well suited to being altered, but it can be done. Some suppliers sell specialized connectors made to pierce the tape and contact the internal conductors, but I'm cheap and I was determined to figure out another way.
NOTE: It may change from one manufacturer to the next, but the inverter that powers the EL tape is typically putting out 120 volts. Don't touch or lick any of the exposed wires or conductive surfaces. You won't like it.**
First, I cut the length of EL tape that I would need, then peeled some of the clear backing off of the backside: 

When you do this, you're likely to damage the electroluminescent layer on the front side of the tape. Everywhere it peels off the colored side is going to be a dark spot. I solve this problem by cutting off a bit more length than I need and just cutting off the damaged portion.
The electroluminescent layer will begin to degrade on contact with air. It will also melt if you attempt to solder anything to it. I solve both of these problems with a cyanoacrylate adhesive called Insta-Cure (a.k.a. Zap-a-Gap or Krazy Glue).
The object is to glue wires to the exposed conductive strips (the darker areas) inside the tape. Use stranded wire for more potential contact area than solid wire. Each wire lead gets a drop of glue and then I push them onto the conductors with a bit of pressure to make sure the wire actually makes contact and isn't insulated from the conductor by a film of glue.
Before sealing it up, this is a good time to turn it on and make sure it actually works. If it doesn't light up, you need to pull the wires off, clean them up, and peel a bit more backing to get at a new, clean patch of the conductors. If it does work, seal it up using more glue to hold down the clear backing to hold the wire in place while the glue cures.
With the EL tape glued in place, I went ahead and laid on even more glue to help seal up the cut edges. Then I used some velcro to hold the inverter and batteries in place inside the forward end and some rare earth magnets to hold the cover onto the left side.
All I need now is to find the best place to display it:
I'm still working on that.
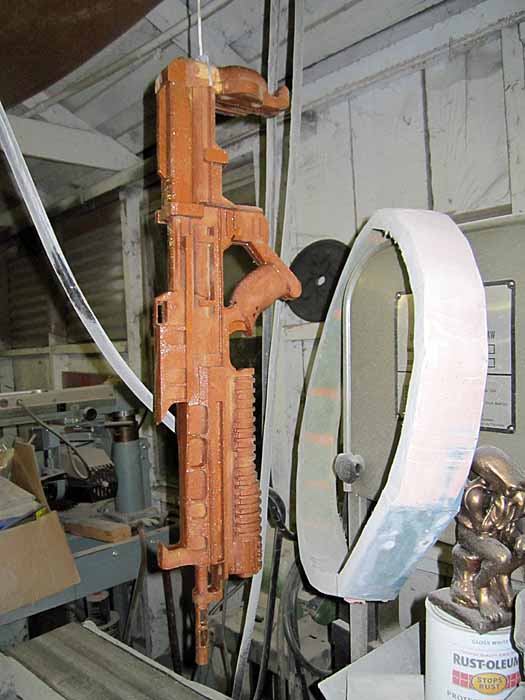
Be sure to subscribe so you don't miss any updates...
*Sometimes I really wonder what goes through people's minds when I drop off trash at the local refuse collection site.
**I know I didn't like it.
This is a great write up.
ReplyDeleteI am so very glad I sent you the model in the first place.
That is one amazing project. It is really easier to do things if you have a cnc machine. You can build things with precision. It is better to search for plasma cutters for sale if you have this kind of project.
ReplyDeleteYou have done a great job. Thanks for sharing this useful and inspiring post.
ReplyDeleteHimes Machinery
Good
ReplyDelete